Tori Roberts
Lighting/Electrical Option
Dr. Kevin Houser
Northeastern United States

Building Statistics Part 1
General Building Data
Building Name | Health & Wellness Care Center (fictitious name)
Location and Site | Northeastern Region of the United States
Building Occupant Name | Cannot be disclosed due to confidentiality
Occupancy Type | Healthcare/Mixed Use Size: 200,000 sq. ft.
Stories above grade/total | 3 levels, all above grade
Dates of Construction | June 2011 - December 2012
Project Cost | $55,000,000
Historical Requirements | Not applicable

North facade perspective view.

South facade perspective view.
Project Team
Project Management | Aegis http//aegis-company.com/projectmanagement/
Architect | Stantec https://www.stantec.com/en
Structural Engineer | O’Donnell & Naccarato https://www.o-n.com/
Civil Engineer | Dewberry-Goodkind, Inc. http://www.dewberry.com/
MEP Engineer | Barton Associates, Inc. https://www.ba-inc.com/
Pool Consultant | Water Technology, Inc. http://www.watertechnologyinc.com/en/
Health & Wellness Consultant | Power Wellness Management https://www.powerwellness.com/
Equipment Consultant | Medequip International https://www.manta.com/c/mmzhs31/me dequip-international-inc
Tele Data | Bala Consulting Engineers, Inc. http://www.bala.com/
Acoustic Consultant | RJC Designs, Inc. http://www.rjcdesigns.com/

Architecture
The Northeast Ambulatory Care Center is a 3-story healthcare facility that is made up of three different areas. These areas consist of a Health and Fitness wing, a Department of Community Affairs wing and a Medical Office Building which is in between the two wings. These three areas are configured into an “L” shaped building. The main entrance to the building is also on the north façade with a canopy made up of a metal composite material panel. This north entrance location and the opposite south façade entrance has a continuous “slice” architectural feature to emphasize the entrances shown in Figure 3. This is a stone veneer wall that runs perpendicular through the building and projects outside of the building shape.
The architectural “slice” at one of the building entrances.
National Model Codes
Uniform Construction Code (State not listed due to confidentiality reasons)
International Building Code, Group B 2009
National Electrical Code 2008
International Energy Conservation Code 2009
International Fuel Gas Code 2009
International Mechanical Code 2009
National Standard Plumbing Code 2009
Barrier Free Requirements Per ICC 2003
Building Enclosure
Building Facade
The building’s exterior materials primarily consist of an integrated system between metal composite paneling and cast stone coping. Amongst these materials on the north façade is an aluminum curtain wall system shown below. Additional types of materials can be found on the west elevation exterior with cast stone coping and zinc wall panel as shown in Figure 5. All of these materials are supported by interior metal studs throughout the whole building structure.
Shading for the southern wall consists of 8’ sunshades on the first-floor window system with a PVDF finish to match the mullions which is shown below.

Aluminum curtain wall system on the north façade.

The integration of materials on the west building façade.

Sunshade section of a typical overhang on the southern façade.
Windows/Curtain Wall
There are four different types of glazing used on the building. The first is a vision IGU PPG SOLARBAN 60 glass with a caribia tint. The second type is a spandrel IGU PPG SOLARBAN 60 with a caribia tint. The third is an acid-etched IGU PPG SOLARBAN 60 with caribia tint. The final glazing type is a clear laminated monolithic glazing. Additionally, there is a glazed aluminum curtain wall system that was installed on the north façade spanning from the three floors of the buildings height.

Roofing
The roofing system consists of a fully adhered ethylene-propylene-diene-monomer (EPDM) covering the entire roof.
Rooftop aerial view.
Sustainability Features
The most sustainable piece to the project was inclusion of a 20,000 cfm energy recovery unit to precondition air for the Health and Fitness center locker rooms and support spaces. This was very important to the client to ensure the best air quality for all the patients and members using the facility.

Locker room with sustainable design considerations.
Building Statistics Part 2
Construction
The Health & Wellness Care Center was a $55,000,000 project that broke ground for construction in June of 2011. This slab on grade, three-story building construction was performed in two different phases. The first phase of construction was the shell and core of the building. The duration of the shell and core construction spanned from June 2011 to substantial completion of phase one in October 2012 and cost a total of $26M. The second phase of construction was the tenant fit out which consisted of three different sections of the building; Health and Fitness, Medical Office Building, and Department of Community Affairs. The duration of the tenant fit-out construction spanned from April 2012 through December 2012 and cost $29M.
Lighting
The facility utilizes fluorescent fixtures as the majority of the lighting equipment. Normal/Emergency lighting is provided throughout all tenant spaces for exiting and illuminating the means of egress. For tenants having a direct exterior exit, that portion of the tenants’ exit discharge immediately adjacent to the exit discharge doorway will also have normal/emergency lighting. All exit signs utilize an LED light source and include integral batteries for emergency power. Fluorescent fixtures that will be used to illuminate the means of egress during an emergency incorporate one lamp having integral battery backup.
Offices, patient treatment rooms, reception areas, waiting rooms, toilets, soiled holding, clean utility rooms, and similar spaces have occupancy sensors for switching lights on and off. For additional control, each area has either multiple switches for discrete adjustment of light level, or dimmers for continuous adjustment of light level depending on specific tenant requirements.
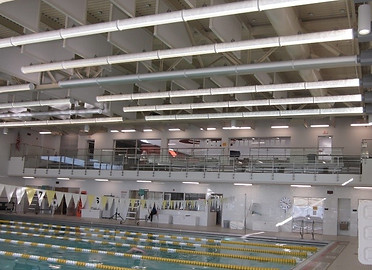
Linear lighting chosen to illuminate the aquatic area.
Electrical
The buildings shell and core electrical infrastructure consists of a three phase 277/480V electrical service and a 4000A switchboard with a termination section, a utility metering section, a main circuit breaker section, and distribution sections. Circuit breakers in the distribution sections of the switchboard provide power to 277/480V, three phase distribution panelboards located in the electrical closets throughout the facility. Power to each tenant space is provided at 277/480V, three phase from the nearest distribution panelboard through a tenant provided sub-meter. Feeders are extended as required by each tenant, from the 277/480V, three phase distribution panelboard to panelboards within each tenant space for further power distribution as seen in the image to the left. Power at 120/208V is derived using dry-type step-down transformers which feed 120/208V panelboards. The feeders and power distribution equipment on the load side of each distribution panelboard including the necessary over current protection in the distribution panelboard is tenant provided.
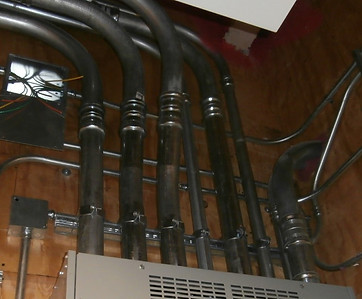
Electrical feeders servicing from the shell and core to the tenant fit-out.
Mechanical
The HVAC scope of work consists of the extension of ductwork from the building’s shell and core infrastructure to specific tenant spaces, installation of variable air volume boxes in supply ductwork, and installation of diffusers, registers and grilles. Specialty systems are installed where required to meet specific tenant needs. The building’s core and shell HVAC infrastructure consist of seven gas-fired rooftop units, ten roof-mounted general exhaust fans and duct risers extended to each floor level as shown in the image below.
The tenant spaces is served by variable air volume (VAV) systems served by the gas fired rooftop units installed as part of the core and shell construction. Main and branch supply ductwork is extended from existing risers and VAV boxes utilize integral electric reheat coils for space temperature control. Main return ductwork is extended from existing risers into each tenant area. Plenum return is used within each tenant space, except for those spaces that require ducted return air systems to meet code requirements. Temperature sensors are installed in each temperature control zone. The tenants’ Direct Digital Control (DDC) system is extended to the existing Building Automation System (BAS) backbone.

Mechanical equipment housed on the roof of the building.
Plumbing
Domestic cold water is extended from 2-inch domestic water risers located within the area of work and is distributed to plumbing fixtures and equipment as required. An electric storage-type domestic water heater is in the area of work for each individual tenant and supplies hot water to plumbing fixtures and equipment as required within the specific tenant area, include fixed water connections for coffee makers in each tenant space. Domestic hot water recirculation systems are installed where required. Domestic water piping is copper and insulated in accordance with applicable plumbing and energy codes.
Sanitary waste piping is extended from plumbing fixtures and equipment in the tenant area of work and is connected to existing 4-inch sanitary waste risers located along structural columns. Sanitary vent piping is extended from plumbing fixtures and equipment as required and connected to existing 4-inch vent risers located along structural columns in the area of work. Sanitary and vent piping installed above grade is cast iron. Sanitary piping installed below grade is either PVC or cast iron.
Water closets, lavatories, and sinks are sensor-operated, hands-free type. All plumbing fixtures are water conserving in accordance with the applicable plumbing codes and comply with ADA regulations where required.
Fire Protection
The fire protection consists of modification and extension of the buildings core and shell sprinkler system to serve each specific tenant. Branch sprinkler piping installed for the core and shell is modified to accommodate new ceilings. The entire sprinkler system is provided in accordance with NFPA 13, local and state codes and applicable standards.
Each tenant space is fully sprinkled. Sprinkler heads in finished ceilings are concealed with white cover plates. Sprinklers in areas without ceilings are standard type, brass and of appropriate orientation.
Structural
The structural system for the Health & Wellness Care Center begins with a 4” concrete slab on grade over 6” of crushed stone for the building. The only exception is an 8” concrete slab on grade over 6” crushed stone located in the Health and Fitness wing where the mechanical heating equipment for the pools is located. The building is a steel frame structure with the east wing having 21 bays and the west wing having 13 bays spanning the curved plan of the building. Many of the bays are of varying lengths. The exterior walls are supported structurally with diagonal bracing on each of the three levels of the building which is shown in the figure to the left. The roofing system consists of a fully adhered ethylene-propylene-diene-monomer (EPDM) that covers the entire roof. A roof screen was constructed on top of the EPDM system which is all supported by metal decking for the building

Diagonal bracing used for the structural reinforcement of the exterior walls.
Telecommunication
The main telecommunications server room is located on the first floor of the building in the west wing. It is interconnected to the second wing and the central area with supporting equipment housed in the electrical spaces as needed throughout the building. The telecom system is connected to the buildings security system as well as the building integration system for tracking of tenant usage of utilities.
Transportation
There is one main elevator core in the center of the building. Additionally, each of the two wings has one elevator. Each of these locations also has stairwells to access each of the three floors. Each of these locations are public elevators and can be used for each of the three areas of the building; Health and Fitness, Medical Office Building, and Department of Community Affairs.

Main elevator core extending from the lobby area for transportation through the building.